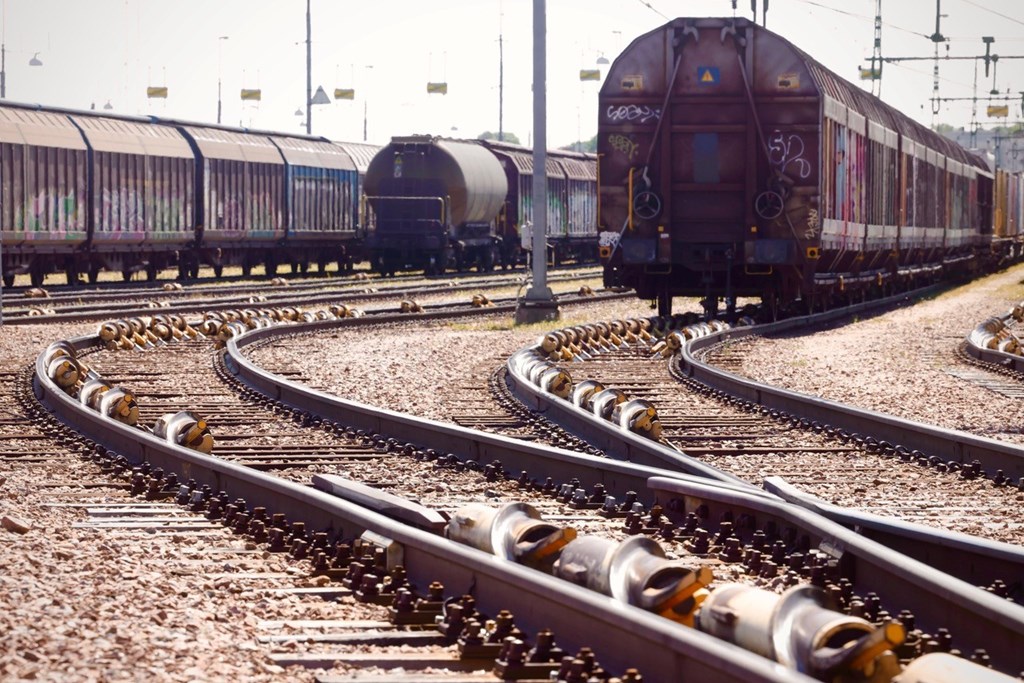
DECEL Brakes for the Future
DECEL AB, with production in Överhörnäs, Örnsköldsvik, specializes in braking systems for freight wagons and continues a long history of technological and service work in sustainable railway technology. The company has a strong local foundation, with a clear focus on energy efficiency and recycling.
In the summer of 2023, Decel was born out of the desire to preserve and renew a technology with roots dating back to the ASEA era – a braking system for freight trains based in Mellansel. The system, which has passed through several industrial giants such as Hägglunds, ABB, and Bosch Rexroth, was at risk of disappearing completely. That’s when Niklas Hörnell stepped in.
“I had been working with the system in the background since 2009 and saw its potential. When there were no further investments, it became a personal mission for me to find a solution. I told Bosch: don’t sell it abroad—contact me, and we’ll find a way forward,” says Niklas, CEO and founder of Decel.
With the support of local industry profiles and a strong will, he succeeded in doing just that. In no time, funding, personnel, and equipment were secured, and in the summer of 2023, they moved to Överhörnäs. At that time, there were four employees. Today, there are nine.
“We have an incredible amount of work right now. It’s clear that there’s a huge need to upgrade and streamline railway logistics,” says Niklas.
Founder Niklas Hörnell runs DECEL with local power and global ambition.
The Old Technology – Outdated and Inefficient
Railway yards are the hub for freight traffic. But in many parts of the world, outdated solutions are still in use:
- Brake blocks – manually thrown under the wheels. They cause extensive damage to wheels, rails, and sometimes personnel, as they can be hurled away.
- Bogie brakes – long mechanical devices that slow down wagons for a few meters, but then lose effectiveness and allow acceleration.
- Diesel-powered locomotives – often used in flat yards to move wagons, resulting in a high carbon footprint, often over 1,000 liters of diesel per day and yard.
“In Kazakhstan, we saw they were still using brake blocks. We had those in Sweden in the 60s. It causes both material damage and health and safety risks,” says Niklas.
DECEL's Solution – Smart, Safe, and Green
Decel’s braking system is designed for marshalling yards where wagons are rolled down from an elevated ramp. Here’s how the technology works:
- Automatic brake control – the system detects speed and applies the exact braking force.
- Constant speed through switch zones – reduces the risk of collisions and increases efficiency.
- No diesel locomotives – eliminating emissions from manual movement.
- Pneumatic control with minimal energy consumption – operation only when needed.
- Circular approach – brakes are repaired, renovated, and reused – often after 30–40 years of operation.
“Energy efficiency in a marshalling yard beats everything else. With our solution, there’s no need for a diesel locomotive, and maintenance is minimal. This is clearly green technology,” says Niklas.
The system is also flexible – each brake is an individual hydraulic system that can be easily adapted. A newly developed simulation tool allows for the entire yard to be designed and the braking behavior tested digitally in advance.
“We can release a 90-ton wagon with a full tailwind in the simulator and optimize the solution before we even begin installation,” says Niklas.
Smart, circular brakes - built to last decades.
Breakthrough in Kazakhstan
Decel’s most exciting market right now is Kazakhstan – one of the world’s key logistics hubs for railway transport between Europe and Asia. After a successful presentation to the state-owned railway company, Decel has signed a supply agreement for pilot systems.
“Their railway yards are heavily outdated and still use technology we left behind in the 60s. There’s a huge need for modernization, and that’s where we come in,” says Niklas.
The process moving forward involves extensive testing, technical approval, and then public procurement. But the potential is large, both technically and commercially.
Georgia might also be joining the customer list, with Decel now participating in an export program focusing on Southeast Asia, alongside the Swedish Energy Agency and Business Sweden. Targeted markets are Indonesia, Vietnam, and Thailand.
“It’s only now that we’re starting to understand how valuable it is to be part of a larger network. As a new member of North Sweden Cleantech, we gain access to contacts and experience that make a difference,” says Niklas.
Local Strength - Global Impact
Despite its global reach, Decel has a long tradition of collaborating with local partners in Örnsköldsvik. All processing, welding, and painting are done by companies like Tordab AB, MPS, and HL Coating. Recycling is an obvious choice – not just as a sustainability strategy but also as a practical solution.
“We are currently renovating brakes that have been in service for over 40 years. They’re going back into service at Swedish railway yards. That’s circular economy in practice,” says Niklas.
When Infranord recently came for training at Decel to learn how to operate the brakes, it became clear that knowledge and technology go hand in hand.
“It’s important for us that our customers understand how the technology works. And it’s appreciated – many like getting a glimpse into a product that otherwise just ‘exists out there’ on the tracks,” he says.
Although Decel is working within a narrow niche, it’s clear that, through local roots and global ambition, they show how sustainable technology can take off – by braking in the right way.