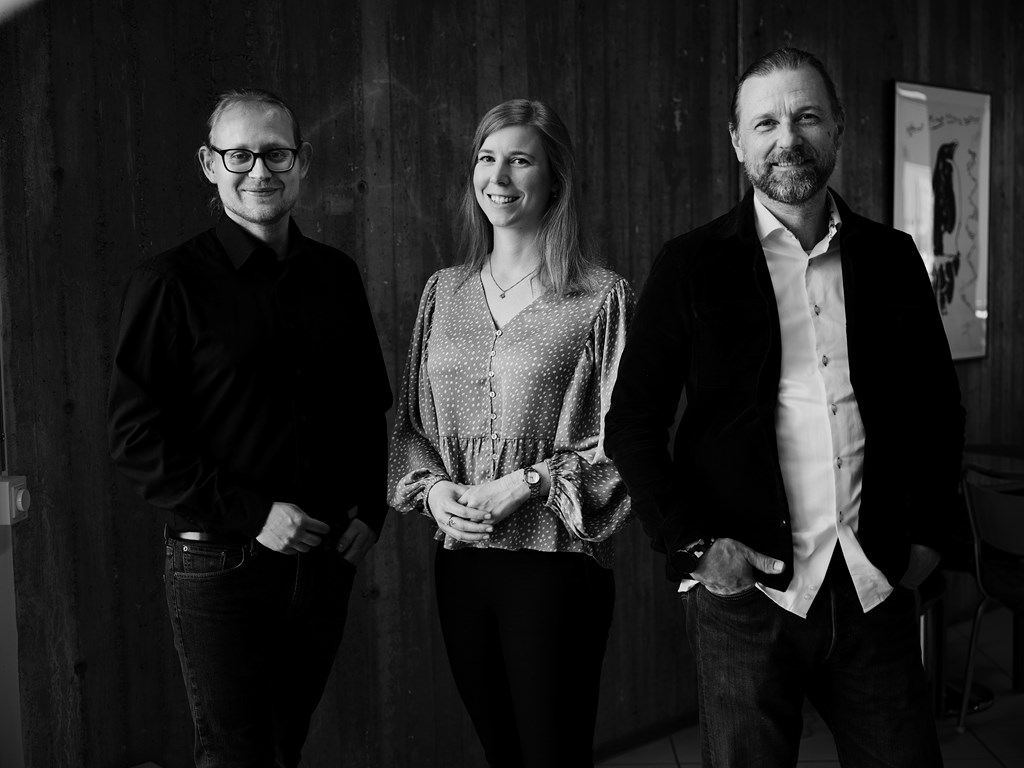
Green Testbeds Part 1: Reselo and the Future of Rubber Manufacturing
We are now starting a series of articles about the important test and demo environments in northern Sweden – a prominent infrastructure that has helped many innovations scale up and take the next step in their development. First up is the biomaterials company Reselo, which is on the way to transforming the rubber industry.
------
Reselo and the Future of Rubber Manufacturing
Birch has long been considered a versatile material, but it is the previously unused by-product – the bark – that proves to be important in the transition to sustainable rubber manufacturing. Through its collaboration with RISE test environments in Örnsköldsvik, Reselo has taken crucial steps towards developing a rubber based on birch bark, which now plays an important role in tire giant Nokian Tyres' ambition to revolutionize the rubber industry.
The product Reselo Rubber is a completely renewable material made from birch bark that comes from residues from the global pulp, paper, and plywood industry. It is unique because it is vulcanizable, making it possible to use in demanding applications such as shoe soles, car tires, and vehicle components, ranging from interior to exterior and seals. Henrik Otendal, CEO and co-founder, talks about the journey that took off through the collaboration with RISE in Örnsköldsvik.
– We made initial contacts in 2019 with Jonas Markusson and Gunnar Westin, who were very enthusiastic about our idea. It was an important first step, and when we later teamed up with RISE in Örnsköldsvik, we were able to produce the first batches of our rubber material, says Henrik.
Henrik's co-founder, Dr. Thomas Baumgarten, is actually a biochemist from Germany. He studied in Germany but moved to Sweden for his doctorate. Thomas then found a postdoctoral position at KTH and the Wallenberg Wood Science Center, where the research focused on increasing the value of biomass – essentially exploring what new things we can do with trees.
From that mission, he came up with the now patented method of birch bark. But it was only a few years later, when he met co-founders Josefine Larsson and Henrik Otendal during the entrepreneur competition Startup Climate Action Challenge, that the innovation really took off and developed into a company.
Then Reselo Took Giant Leaps
In the startup phase, an important part of the collaboration with RISE was to develop and optimize the manufacturing protocol. Reselo had an early idea of what the process would look like, but thanks to guidance from Jonas and Gunnar's team, they were able to adjust the protocol and avoid some of the common pitfalls.
This made the whole project take giant leaps in a way that would not have been possible otherwise.
– They suggested that we cut down on certain parts and remove some chemicals entirely, which allowed us to enter a much more optimized version from the start and avoid making some initial mistakes, explains Henrik.
RISE has also been involved in conducting techno-economic analyses. This was important for Reselo, which got a clear picture of the costs and how production can be scaled up. These insights allowed the company to develop a product calculation that was both technically and economically sustainable.
– We could not have made the step from lab to production without their help. It also allowed us to show our customers early on that we have a robust and scalable process, which has been crucial for quickly getting the business going, continues Henrik.
Key Player with Nokian Tyres
Reselo has a lab and office at Greenhouse Lab on the KTH Campus in Stockholm, a cluster consisting of young chemistry companies, students, and researchers, including in bio-innovation, an environment that suits Reselo perfectly.
The company today has several major customers, including Nokian Tyres, which sees Reselo as a key factor towards their goal of having 50 percent of the raw materials in their tires renewable or recycled by 2030.
The tire giant also expects that Reselo Rubber will help improve the performance of the tires.
The company also collaborates with Volvo, Scania, and Polestar, as well as a number of shoe manufacturers that we "definitely know the names of" but which are still secret.
– Of course, it feels fantastic and inspiring that so many believe in our product. It has also gone faster than we thought, but we started early with selling in and building relationships with customers, which aroused great curiosity. The rubber industry has not changed much in over 120 years, so there is a great opportunity for us here, says Henrik.
Collaboration with SLU in Umeå
Reselo uses birch bark from, among others, sawmills and paper mills, which is separated into three components: suberin, betulin, and lignin. The suberin is used to make the rubber, while the other material streams are used for other high-value applications in biopharma, cosmetics, and other industrial chemical applications.
– We use over 90 percent of the raw material, and what is left works excellently as fuel, which makes the process very efficient and keeps the cost of the final products down, explains Henrik.
Currently, Reselo is also collaborating with the Swedish University of Agricultural Sciences, SLU in Umeå, which helps with drying the bark, and the company also has a pilot plant through a production partner with a capacity of about 100 tons per year.
– SLU has played an important role in the process chain, adds Henrik.
Reselo continues to develop its process and build strong collaborations, both in Sweden and internationally.
– We see enormous potential here. Our material can fully replace fossil rubber, and we want to collaborate with companies that share our vision of a more sustainable future, concludes Henrik.
Caption: Reselo was founded by Thomas Baumgarten, Josefin Larsson, and Henrik Otendal. The innovation is based on research from KTH and has been developed with the help of RISE in Örnsköldsvik.
Click here to read the second article in the series, "BTC in Umeå Attracts Global Customers"!